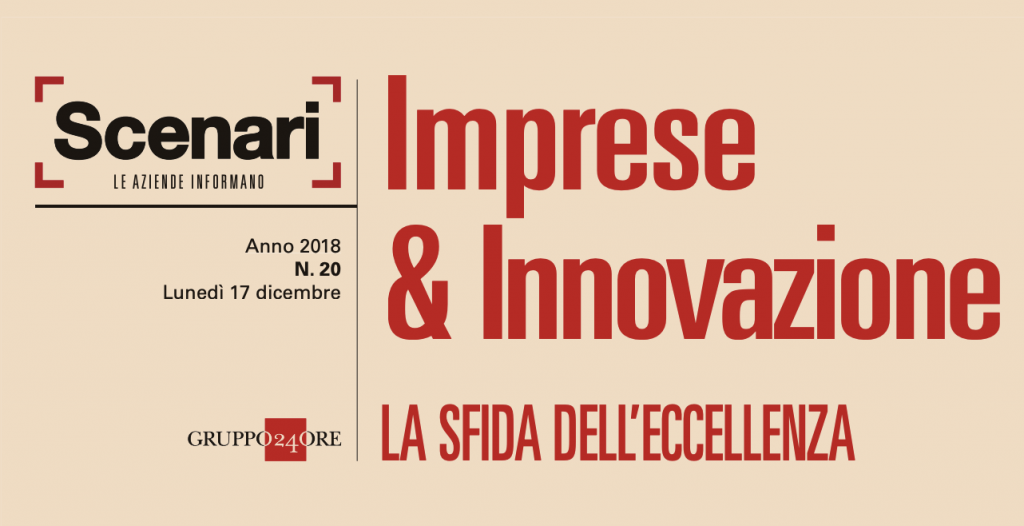
Businesses & innovation, SAGA's case history
We are proud to publish this beautiful Scenari Nazionali focus feature on the history of and the new challenges faced by SAGA
MESTRE. Investments for one point five million a year – reaching in some cases two million. Know-how regeneration abilities to tackle the ever-new challenges posed by inherently advanced sectors, such as the automotive industry, and an entrepreneurial flair that has translated into forward thinking, restructuring the company and giving it a strategic outlook to face the near future with confidence, with a view to expanding into new markets. These are the features that make of Saga a partner in the field of moulds and moulding for the development of innovative and superior quality solutions, using, among others, amorphous alloys for the creation of products with top-class technical properties. Today, due to the costs involved, this is still a niche market which, however, is well poised for growth. Founded forty years ago as a mould and moulding company for thermoplastic materials, it has managed, over its many years of activity, to accept skilfully and professionally any challenge coming from the market. “In response to a market that expects one-stop partners able to take care of all-round product development – explains the company’s commercial director, Giancarlo Peruzzo – we have evolved by perfecting the ability to manage complete production processes as prime contractors, even in the case of metal, electronic or other components, thanks to specialized partners.” Among the company’s strong points is injection moulding of amorphous metal alloys, first experimented with back in 2006, when Saga signed a joint venture agreement with Liquidmetal Technologies Inc. Today, thanks to an exclusive collaboration agreement for Europe, it implements prototypes and components using a new generation press built by Engel to Liquidmetal’s specifications. The Bmg technology combines a melting phase, performed in a vacuum chamber to avoid contamination with oxidising elements that could affect the mechanical performance of the end piece, and with injection of the molten alloy into the mould, followed by moulding. “While the related costs are still rather high, this technology ensures superior performance in terms of mechanical resistance and corrosion, hardness, flexibility, reduced thickness and absence of deformations – explains the director – which is particularly interesting in the field of small-medium sized technical components, for innovative sectors such as the automotive or consumer electronics industries.” Constant exchanges with top international industry players allow Saga to be consistently proactive and innovative – and an acknowledged leader of the market. With a workforce of 100 employees, the company has consolidated relationships with various departments of the University of Padua (Chemistry, Pharmacology and tissue regeneration), with the CNR of Padua (Metallographic office), and with the Padua-Matech Science Pole (innovative materials) for the purpose of experimenting with possible processing and application options for new materials. Interesting results have been achieved in the processing of plastic materials containing nanofillers and biocompatible polymers, and recently, in the analysis of the possible uses of graphene. Going back to production aspects, the mould design and product engineering phase, carried out in collaboration with the customer and using Fem prototypes and analyses, enables the supply of tailor-made solutions. This process can resolve in advance all issues linked with product creation – guaranteeing an optimal end result